Manufacturing Workshop
Our Equipment
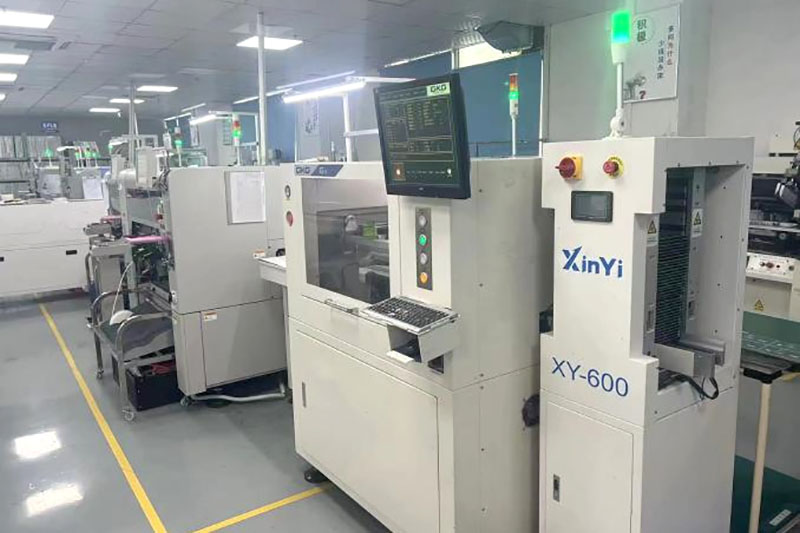
semi-automatic solder paste printing machine
There are 5 high-precision semi-automatic solder paste printing machines. These high-precision semi-automatic solder paste printers are critical to ensuring accurate and reliable application of solder paste during PCB assembly. Each machine is equipped with advanced features for efficient and accurate printing.
A critical component in the solder paste printing process is the stencil. The stencil acts as a template to direct the solder paste or adhesive onto the appropriate pads on the PCB. It plays a vital role in maintaining the precise dimensions and alignment required for error-free welding.
The automated nature of these machines greatly increases production efficiency. With their high precision and speed, they are capable of printing solder paste or adhesive on multiple PCBs simultaneously. Not only does this save time, it also reduces the risk of human error and ensures consistent and reliable solder paste application.
automatic multi-function high-precision placement machines
There are 8 Korean Samsung automatic multi-function high-precision placement machines. The fully automatic multi-functional high-precision placement machine is the most advanced equipment used in the electronics manufacturing process. These machines play a vital role in accurately placing components on printed circuit boards (PCBs) with extreme precision and efficiency.
One of the main features of these machines is their automatic function. They are equipped with highly advanced vision systems, cameras and sensors, enabling them to precisely detect and identify components on reels, pallets or tubes. These machines automatically pick components of various shapes and sizes from designated sources and place them in the correct location on the PCB.
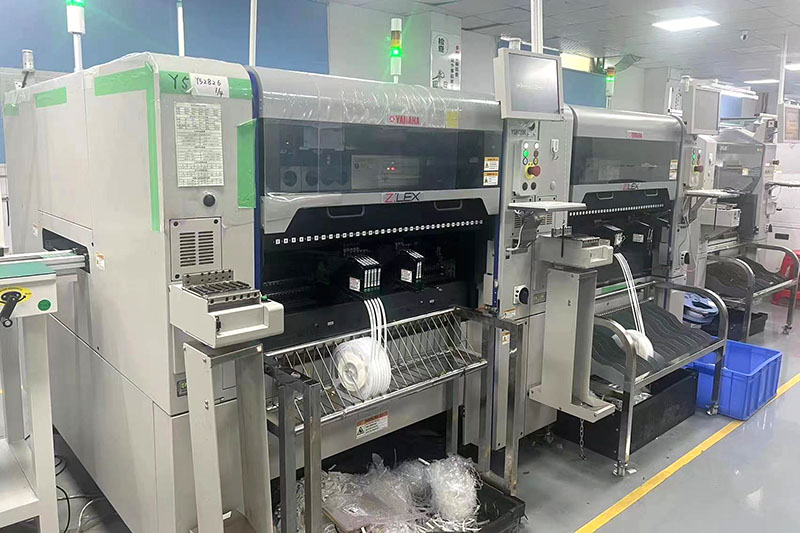
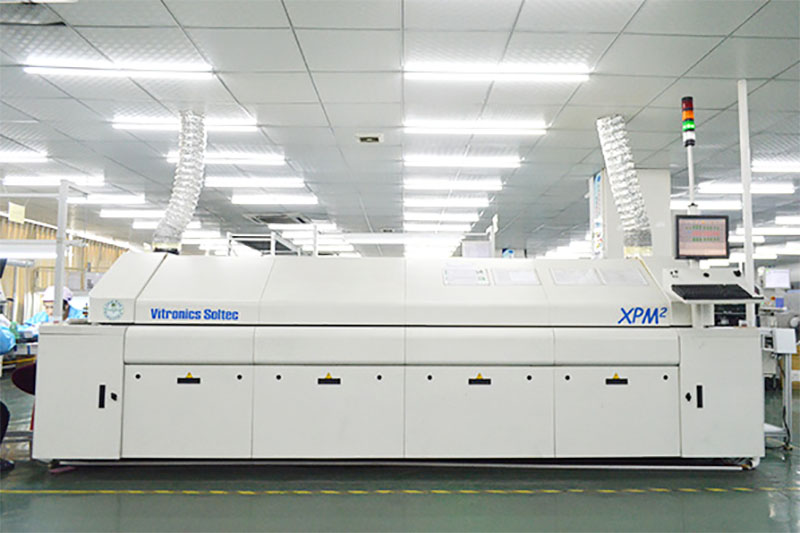
Fully automatic infrared hot air reflow oven
Fully Automatic Infrared Hot Air Reflow Oven is an advanced and innovative solution for precise soldering of electronic components onto PCBs. It is designed to meet international standards and follows a predefined temperature profile, ensuring accurate and consistent temperature control during the soldering process.
One of the main advantages of this type of reflow oven is its ability to prevent thermal damage and deformation of the PCB and its components. A precise temperature control mechanism ensures that the soldering process is performed within the recommended temperature range, minimizing the risk of overheating and thermal stress on delicate electronic components.
The infrared heating technology used in the reflow oven can heat the PCB assembly quickly, uniformly and energy-efficiently. Infrared radiation and forced hot air convection ensure that heat is evenly distributed across the PCB and components, reducing the possibility of localized hot spots or thermal variations. This even heating promotes consistent soldering and minimizes the chance of heat damage.
AOI inspection
AOI inspection, also known as automated optical inspection, is a critical quality control process used in welding production. Based on optical principles, it uses advanced imaging technology to accurately detect and identify common defects that occur during welding.
One of the main advantages of AOI inspection is the ability to detect defects with high precision and speed. The optical system captures a high-resolution image of the welded part, allowing sophisticated algorithms to analyze it and compare it to required specifications. This digital inspection process eliminates operator subjective interpretation, ensuring consistent and reliable defect detection.
AOI inspection can identify a variety of common defects encountered in soldering production, including solder bridges, insufficient solder, insufficient solder paste, misalignment, missing components, and tombstoning. Failure to pay attention to these flaws can lead to malfunctioning or unreliable welding products with serious consequences for different industries.

Quality Inspection
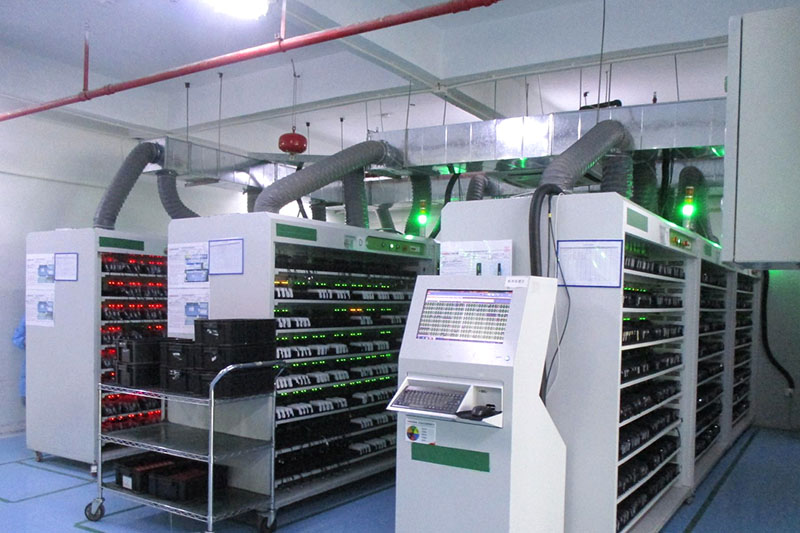
Aging test
At our company, we take great pride in our commitment to providing first-class products and service. One of the key processes that differentiates us from our competitors is our rigorous aging testing of power stations. This testing is an important part of our quality control measures to ensure that only the highest quality products reach our customers.
Our burn-in testing process involves subjecting each power plant to a range of challenging conditions and stressors, simulating real-world usage and environmental factors. These conditions include high temperatures, humidity, voltage fluctuations, and prolonged operation. By subjecting our power stations to such rigorous testing, we can uncover any potential weaknesses or issues that may arise over extended periods of use.
In addition to our rigorous testing process, we are also known for our unwavering commitment to technical excellence. Our team of highly skilled and dedicated professionals is always ready to assist our clients with any technical query or issue they may have.
ATE testing
ATE testing is an essential part of the quality control process in integrated circuit manufacturing. It encompasses a wide range of test methods and techniques designed to ensure the integrity and reliability of integrated circuits.
One of the main goals of ATE testing is to evaluate the functional performance of integrated circuits. This involves checking how the circuit behaves and responds under different operating conditions, such as different voltage levels, frequencies and data inputs. By thoroughly examining the functionality of a circuit, manufacturers can identify any potential defects or failures that could affect its performance or reliability.
ATE testing also focuses on verifying the electrical characteristics of integrated circuits. This includes measuring parameters such as voltage levels, current consumption, signal timing and noise levels. By accurately evaluating these electrical characteristics, manufacturers can ensure that integrated circuits meet required specifications and operate within acceptable limits.
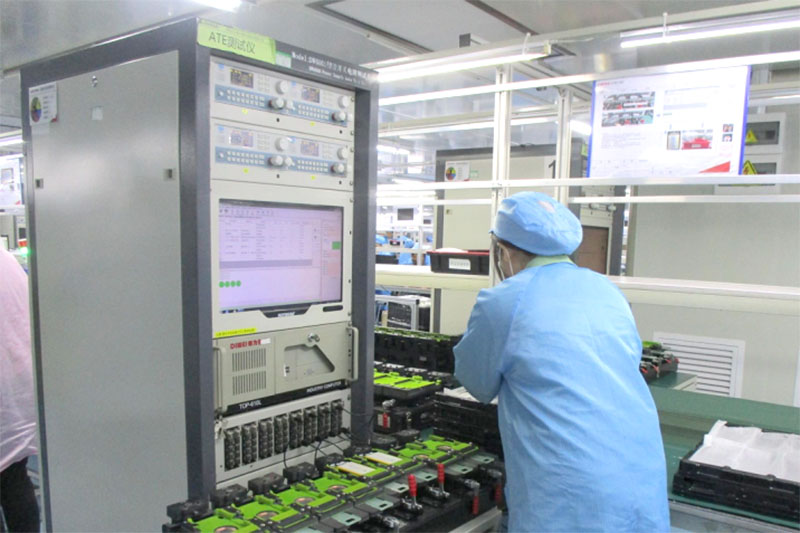